Boost Your Criteria with Expert Welding Inspection Milwaukee Services
Understanding the Relevance of Welding Assessment in Ensuring Structural Integrity
Welding inspection plays an essential duty in maintaining structural stability within the building market, offering as an important secure versus possible failures. By systematically recognizing common defects-- such as porosity and insufficient fusion-- assessments not only maintain high quality requirements but also make sure conformity with safety and security guidelines.
Duty of Welding in Building

In enhancement to architectural applications, welding is integral in the fabrication of both intricate and massive components. It permits the personalization of parts, allowing designers and engineers to bring their layouts to fulfillment. The flexibility of welding techniques, including MIG, TIG, and arc welding, enables the efficient joining of various materials and densities, accommodating specific project demands.
In addition, the improvement of welding technologies has actually led to enhanced efficiency and precision in building processes. Automated welding systems boost efficiency while lowering human error, thereby advertising better outcomes. The function of welding in building prolongs past plain setting up; it is a crucial element in making sure the safety and security, durability, and overall stability of structures, highlighting its significance in the modern-day construction landscape.
Usual Welding Defects
The integrity of bonded frameworks is dramatically affected by the existence of issues that can jeopardize their performance and safety and security. Usual welding flaws consist of porosity, insufficient blend, undercutting, and slag additions, each of which can badly affect the general stamina and longevity of bonded joints.
Porosity takes place when gas bubbles are entraped in the weld steel, causing lowered tensile strength. Insufficient fusion arises when the weld metal does not effectively bond with the base metal, leading to weak joints vulnerable to failure. Damaging, a groove that forms beside the weld, can minimize the efficient cross-sectional area, enhancing the risk of crack. Slag inclusions happen when non-metallic products come to be trapped in the weld, leading to stress focus points that might launch fractures.
Other issues, such as too much spatter and imbalance, can additionally add to structural weaknesses. Determining and resolving these problems during the welding procedure is crucial to make sure the integrity of the final structure. Understanding of these common welding problems is essential for engineers and assessors to keep the stability of welded frameworks and ensure lasting security and performance.
Advantages of Welding Evaluation
Ensuring the integrity of welded structures counts heavily on the efficiency of welding evaluation procedures. The primary advantage of welding inspection is the early detection of potential issues, which can considerably minimize the danger of devastating failures. By recognizing problems such as cracks, insufficient useful source combination, or porosity prior to they escalate, evaluation processes assist preserve the security and reliability of structures.
Moreover, welding evaluation improves conformity with industry requirements and laws. Following these demands is vital for preventing lawful repercussions and ensuring that tasks meet required safety methods. This conformity additionally fosters a society of quality control, advertising finest techniques among welding personnel.
In addition, routine evaluation can cause set you back financial savings over time. By mitigating the likelihood of rework or fixings as a result of welding problems, organizations can assign resources much more efficiently, ultimately boosting performance.
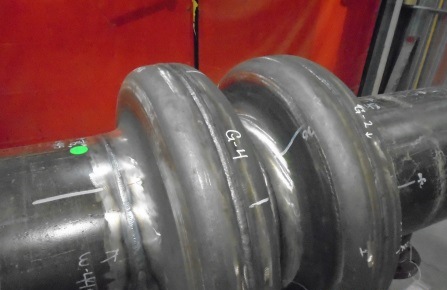
Inspection Techniques and Criteria
Effective examination strategies and criteria are vital components of keeping the stability of bonded structures. Typical inspection methods consist of aesthetic assessment, ultrasonic testing, radiographic screening, and magnetic particle screening.
Visual assessment is frequently the very first step, allowing inspectors to identify surface issues such as splits or inappropriate grain shapes. Ultrasonic screening uses high-frequency acoustic waves to detect interior imperfections, while radiographic testing makes use of X-rays or gamma rays to expose surprise variances within the weld. Magnetic fragment testing works for detecting surface and near-surface problems in ferromagnetic products.
Requirements play a vital duty in guiding these examination procedures, with companies such as the American Welding Culture (AWS) and the International Company for Standardization (ISO) offering thorough guidelines. Conformity with these standards not just makes sure the top quality of welds but likewise fosters depend on among stakeholders in the architectural honesty of the completed item. Abiding by recognized inspection methods and requirements is essential this post to achieving long-lasting and reliable welded frameworks.
Regulatory Compliance and Safety
Governing conformity is important for safeguarding the security and honesty of welded structures. Abiding by well-known codes and criteria, such as those set by the American Welding Society (AWS) and the American National Criteria Institute (ANSI), ensures that welding techniques fulfill stringent security and high quality requirements. These guidelines are made to stop failings that can cause tragic events, injuries, or loss of life.
Conformity with these guidelines includes normal assessments and analyses throughout the welding process. Certified inspectors assess welds for high quality, adherence, and strength to requirements, ensuring that any kind of discrepancies are promptly addressed. This aggressive method not only visit the website improves the architectural stability of bonded elements however also reduces risks related to non-compliance.
In addition, regulative bodies often call for documentation of assessments and compliance documents, which function as legal evidence of adherence to safety and security standards. Business that focus on regulative conformity not only shield their labor force and clients however also improve their reputation within the sector. Ultimately, understanding and applying these policies is critical for any type of company aiming to keep high safety requirements and achieve long-lasting operational success in welding techniques.
Final Thought
In verdict, welding inspection plays an essential duty in keeping structural integrity within the construction industry. Eventually, a commitment to strenuous welding inspection is essential for safeguarding both the workforce and the honesty of constructed structures.
The flexibility of welding methods, consisting of MIG, TIG, and arc welding, permits for the effective signing up with of different materials and densities, catering to specific project needs.
Ensuring the stability of bonded frameworks relies greatly on the effectiveness of welding evaluation procedures (Welding Inspection Milwaukee). In recap, the advantages of welding inspection are diverse, vital for ensuring structural stability and operational quality

Adhering to established codes and criteria, such as those established by the American Welding Society (AWS) and the American National Requirement Institute (ANSI), ensures that welding practices fulfill rigorous safety and high quality requirements. Inevitably, a dedication to rigorous welding assessment is necessary for protecting both the labor force and the honesty of constructed structures.